RexGrains (Recrystallization)
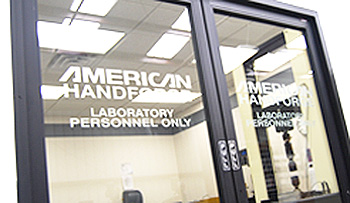
Recrystallization is a word that comes up often in our customer's requirements. Some customers specify just "a little" on the surface or that no recrystallization is allowed with their order.
The key thing is the "re" letters in front of the word re-crystallization. It means "happened again" crystallization. Somewhere in processing the ingot stock and finished forging, an unplanned recrystallization occurred. In order to appreciate what it is, the following example will help in explaining.
One must remember that all metals are crystalline in nature. This is one of the basic requirements for being a metal in the first place. When molten aluminum is cooled and begins to look like a solid, it likes to line-up and attracts other aluminum molecules in a regular pattern. When the metal is carefully cooled (Job of our cast ingot suppliers) to room temperature, the molecules arrange themselves very nicely in a pattern of cast crystalline "grains". This is a short story of what is happening. Normally you can't see these grains because it requires special preparation of the surfaces to see them- but be assured, they are there, nevertheless. In the ingot we obtain, the grains are more or less like little compacted "bb's". They have no general preferred direction In the ingot, except the basic crystal structure pattern you may have seen on other materials.
In the forging process at American Handforge, we take these small original ingots of particular alloy crystalline grains and make them into a more ordered structure. This new ordered structure with elongated grains is "better" than the original cast form. Through the hot working process we reform the original grains into different sizes and shapes depending on how much upsetting and drawing has been done and which direction finally arriving at the ordered size and shape. This process is known as developing a "wrought" structure as opposed to the original cast structure. The grain's volume doesn't get any bigger; they're just longer and perhaps "flatter". This establishes the basic wrought structure and pre-dominate grain directionality of our products. One may think visually it is similar to the appearance in pine boards. By experience we learn the strongest directions are established by the grain direction and basic grain size. The general rule is that the smaller the grains, the stronger the material. So now we have managed to hot forge to the required size our order calls for, but have we met all the requirements?
There is a condition which can occur that under some special conditions may sometimes be detrimental on some forgings. It is known as "Recrystallized Grains" or sometimes as recrystallization, or to some, Rexgrains. What has happened as the result of processing is the planned structure of the original ingot may have gone through an unscheduled change in the grain structure. In the forging process our job is normally to change (squeeze-form) its original size and change the grain direction to what was ordered. Since the planned structure was already a crystalline form, we call this event "Re"-crystallization, meaning it happened "again". The first crystallization process occurs in the solidification or beginning back in the casting operation. This may result in the possible undesired change in basic structure of the forging. Normally one cannot see or detect it by any inspection visually. The forgings must be etched or section taken from the end and prepared to show the condition. This is known as macros etch inspection.
What the recrystallization does basically is to affect the strength of the material. When this occurs, the resulting recrystallized grains are almost always larger. These larger grains are not as strong. Sometimes they can get very large. Forging grains are like the wires in cable. Smaller wires usually mean higher strength. For some alloys, there can be detrimental effects such as fatigue and corrosion performance. Since a majority of our material winds up in aircraft, we at American Handforge and our customers are concerned and vigilant for this condition. In some alloys, recrystallization can adversely affect the visual appearance in anodize, so that is monitored also.
Recrystallization is caused by having the forging temperatures too cold. Too cold can mean starting out with the forging stock too cold or forging too long and letting the material cool off and below its "recrystallization" temperature. The temperature of the tooling (flat forging dies) can also make the situation worse. Our flat die tooling must be heated up temperatures specified, or you may run the risk of developing the recrystallized condition at the surface of the forging. Fortunately most aluminum alloys are reasonably "tolerant" and their chemistry has been chosen to resist recrystallization, but it can occur if you are not vigilant and carefully control the process. Our operating practices are issued and actively monitored with control of the recrystallization specifically in mind. American Handforge prides itself with the procedures and controls in place, thereby insuring consistent quality in the finished product.
For those that would like to know more, the recrystallization actually takes place during the solution heat treat cycle later in the process. It's like exposing film. The "picture" only appears during the film developing. Recrystallization requires heating the forging to the higher temperatures necessary for solution heat treat in order to develop the completely new recrystallized grain structure. Since most of our forgings are heat treated, the condition if potentially there, will eventually show up. Examining the forgings for recrystallization just after final forging operation will not show a recrystallized structure.