Vertical Integration Benefits
American Handforge is vertically integrated which allows us to expand our business into areas that are at different points on the same production path.
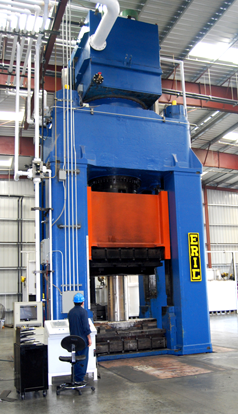
Vertical integration helps us reduce costs and improve efficiency by decreasing transportation expenses and reducing turnaround time, along with these advantages:
Increased Quality: American Handforge processes are controlled and maintained in-house preventing long lead times, delays, and quality problems typical when using multiple suppliers.
Shorter Lead Times: Multiple suppliers increase the amount of product transport time from one location to another, adding cost without adding value. All functions under one roof means more efficient production and shorter lead times, cutting out non-value added cost.
Reduced Delays: Vertical integration means more control over the entire process. Multiple suppliers often result in unforeseen delays when an outsourced project runs behind.
Convenience: Single source means you don't have to spend time coordinating, tracking, and shipping product from one supplier to another. At American Handforge, we do it all in-house, saving you time and frustration.
Save Time: Stop wasting time coordinating production with multiple suppliers. American Handforge can handle your job from start to finish, from raw material to shipping, saving you time and money.
Raw Materials
American Handforge stocks various types of aluminum, stainless steel and titanium alloys so we have product in stock when you need it, reducing lead time and delivery schedules. That means faster quotes, shorter lead times, and quicker delivery to you.
American Handforge commonly stocks millions in raw material in various shapes, sizes, and configurations to help ensure quick turnaround when you need it.
Sawing
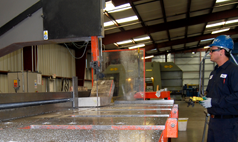
The sawing operation is an important part of the Vertical Integration process at American Handforge. The sawing operation consists of the cutting of initial stock before forging. Precision cuts allow us to minimize any waste of raw material, reducing your parts' end cost.
American Handforge controls the speed, feed rate and pressure at which the blade is fed into the material in order to effectively and efficiently process them. We have developed optimal matrix patterns for all the materials that we process so that we eliminate mistakes and save you money keeping your project on schedule.
Forging
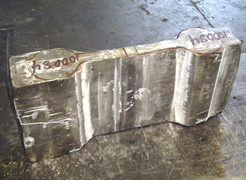
Different products require different metalworking processes. American Handforge provides open die forgings, special shape or bent forgings, and forged rings. Depending on your product needs and specifications, we are happy to work with you in finding your solution.
Forgings and special cut forgings, American Handforge can process your material in a way that will optimize the performance characteristics. Whether cold work, cross-grain, hot forge, upset, upset & cross-grain or warm work, talk to us about which method will work best for you. Learn more about Forging.
Forging Techniques
Cold Working (FIA) — Permanent plastic deformation of a metal at a temperature below its recrystallization point—low enough to produce strain hardening. Usually, but not necessarily, conducted at room temperature. Also referred to as cold forming or cold forging. Contrast with hot working.
Cold Stamp (CDA): To restrike a forging cold in order to hold to closer tolerance, sharpen corners or outlines, reduce section thickness, flatten some particular surface, increase hardness, or add lettering.
Cross Forging (FIA) — Preliminary working of forging stock in alternate planes, usually on flat dies, to develop mechanical properties, particularly in the center portions of heavy sections.
Hot Forging (FIA) — Same as hot working—plastically deforming an alloy at a temperature above its recrystallization point, i.e., high enough to avoid strain hardening.
Hot Press Forging (CDA): A method of forming parts by pressing a heated slug, cut from wrought material, in a closed–impression die.
Upset & Cross-Grain Forge: This method of forging is a combination of Cross-Grain forging in that the work is done on alternate plains, but also as in Upset Forging it is used to increase the cross-sectional area of a portion or all of the stock.
Upset Forging (FIA) — (1) A forging made by upsetting an appropriate length of bar, billet or bloom. (2) Working metal to increase the cross-sectional area of a portion or all of the stock. (3) A forging formed by heading or gathering the material by pressure upon hot or cold metal between dies operated in a horizontal plane. This method is not used as frequently for copper alloys as it is for steels for example due to the ability of copper to be easily extruded.
Warm Forging (FIA) — Deformation at elevated temperatures below the recrystallization temperature. The flow stress and rate of strain hardening are reduced with increasing temperature; thus, lower forces are required than in cold working. For steel, the temperatures range from about 1000° F to just below the normal hot working range of 1900 to 2300° F.
It's important when designing new product or redesigning existing product that you select the process that will deliver the right material properties for you. Our vast forging capacity means American Handforge can handle your work, whether it's an order of 1000 or 1.
Heat Treating
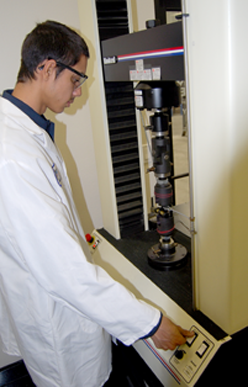
American Handforge ability to handle your needs in house means single-source convenience you can rely on. Further, since it's all done under one roof, you benefit from increased quality, faster delivery, and consistency throughout the process.
Properly heat treating your material is key in getting the right material characteristics for your process. American Handforge has state-of-the-art controllers.
Our furnaces are periodically surveyed and maintained to ensure set point accuracy and variation within the chamber meets our standards. This results in better control of processing parameters which, in turn, translates to optimum properties to meet your specifications. American Handforge is continually evaluating our heat treating processes to maximize material performance.
Knowing the right time and temperature relationships ratios are the essential in giving you optimal material properties. Our services include annealing and or stress relieving, quenching, and solution annealing. These services contribute to our reliable delivery record. Learn more about Heat Treating.
Testing
American Handforge provides testing for mechanical properties (tensile-yield-elongation), grain size, hardness, and conductivity.
Non-destructive test (NDT) services such as dye penetrant, ultrasonic, and radiographic testing round out the services that American Handforge can provide for you.